Hydraulic test is a test method used to check the tightness and strength of equipment such as containers and pipelines.
Its principle is to use the incompressibility of water, apply a certain pressure after the equipment is filled with water, and observe whether the equipment has leakage, deformation, etc., so as to evaluate whether the performance of the equipment meets the requirements.
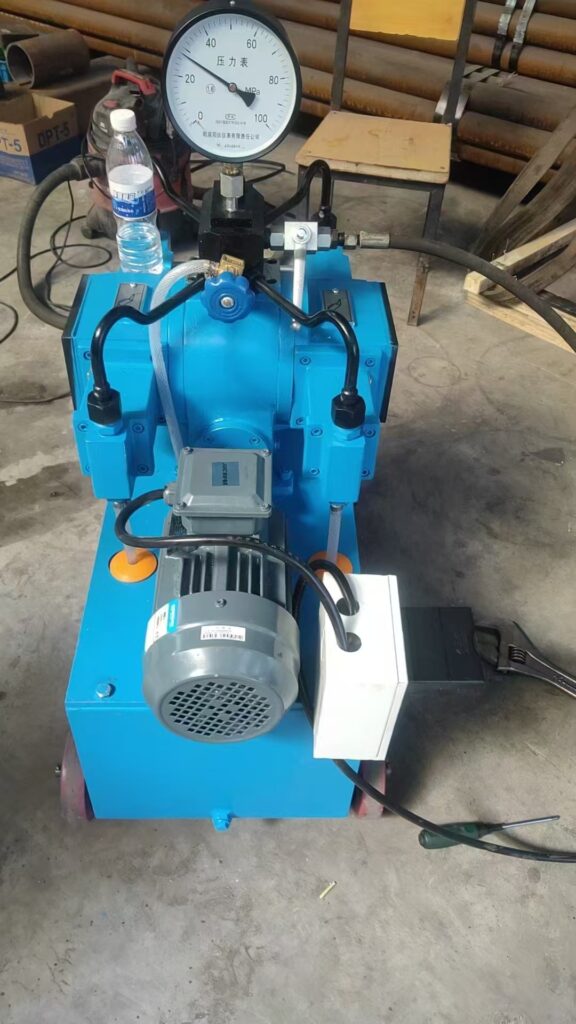
Method
Pre-test stage
Raise the water pressure in the pipeline slowly to the specified test pressure and keep the pressure stable for 30 minutes. If there is a pressure drop during this period, water can be injected to replenish the pressure. The pressure should not be higher than the test pressure;
Check whether there is water leakage or damage at the pipeline interface and accessories;
If there is water leakage or damage, stop the pressure test in time, find out the cause and take corresponding measures before retesting the pressure.
Main test stage
Stop water injection and pressure replenishment, stabilize for 15 minutes. After 15 minutes, when the pressure drop does not exceed the allowable pressure drop value, reduce the test pressure to the working pressure and keep the constant pressure for 30 minutes. Perform an appearance inspection. If there is no water leakage, the water pressure test is qualified.
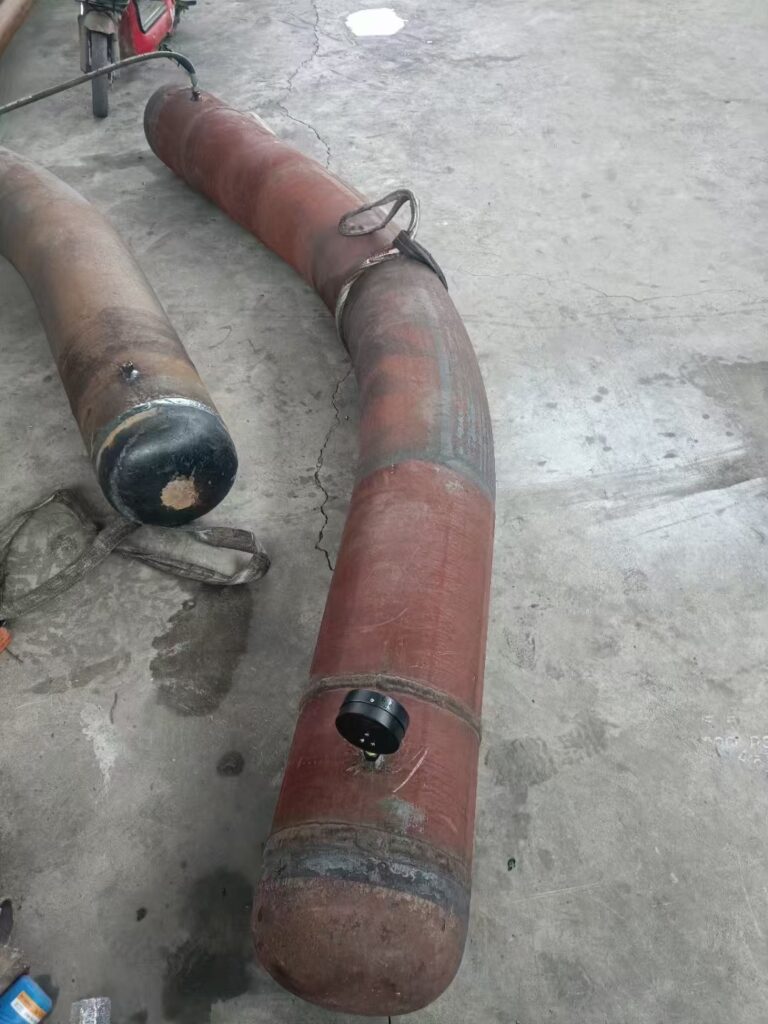
Test steps
Test preparation:
The equipment to be tested should be installed with corresponding connecting pipes, valves, etc., and ensure that the connection is firm.
Remove debris, rust and other impurities inside the equipment to ensure that the equipment is clean.
Install the pressure measuring instrument and calibrate it to ensure its accuracy.
Water injection and exhaust:
Inject water into the equipment and open the exhaust valve at the same time to exhaust the air in the equipment. Because air is compressible, if there is residual air in the equipment, it will affect the accuracy of the test results.
Pressure boosting process:
Slowly increase the pressure, the speed should not be too fast, and it is generally controlled within a certain pressure range per minute (such as 0.3-0.5MPa/minute).
During the pressure boosting process, pay attention to observe whether the equipment has abnormal sounds, jitters or leaks.
Pressure holding stage:
When the pressure reaches the test pressure, stop increasing the pressure and maintain the pressure for a period of time. This time varies according to different equipment and standards, generally 10-30 minutes.
During the pressure holding period, carefully check whether there are leaks in the various connection parts, welds, seals, etc. of the equipment. You can use direct observation or auxiliary tools such as test paper and leak detection liquid to check.
Pressure reduction and drainage:
After the pressure maintenance is completed, slowly reduce the pressure, and the pressure reduction speed should not be too fast.
After the pressure reduction is completed, drain the water in the equipment, and pay attention to prevent water backflow during the drainage process
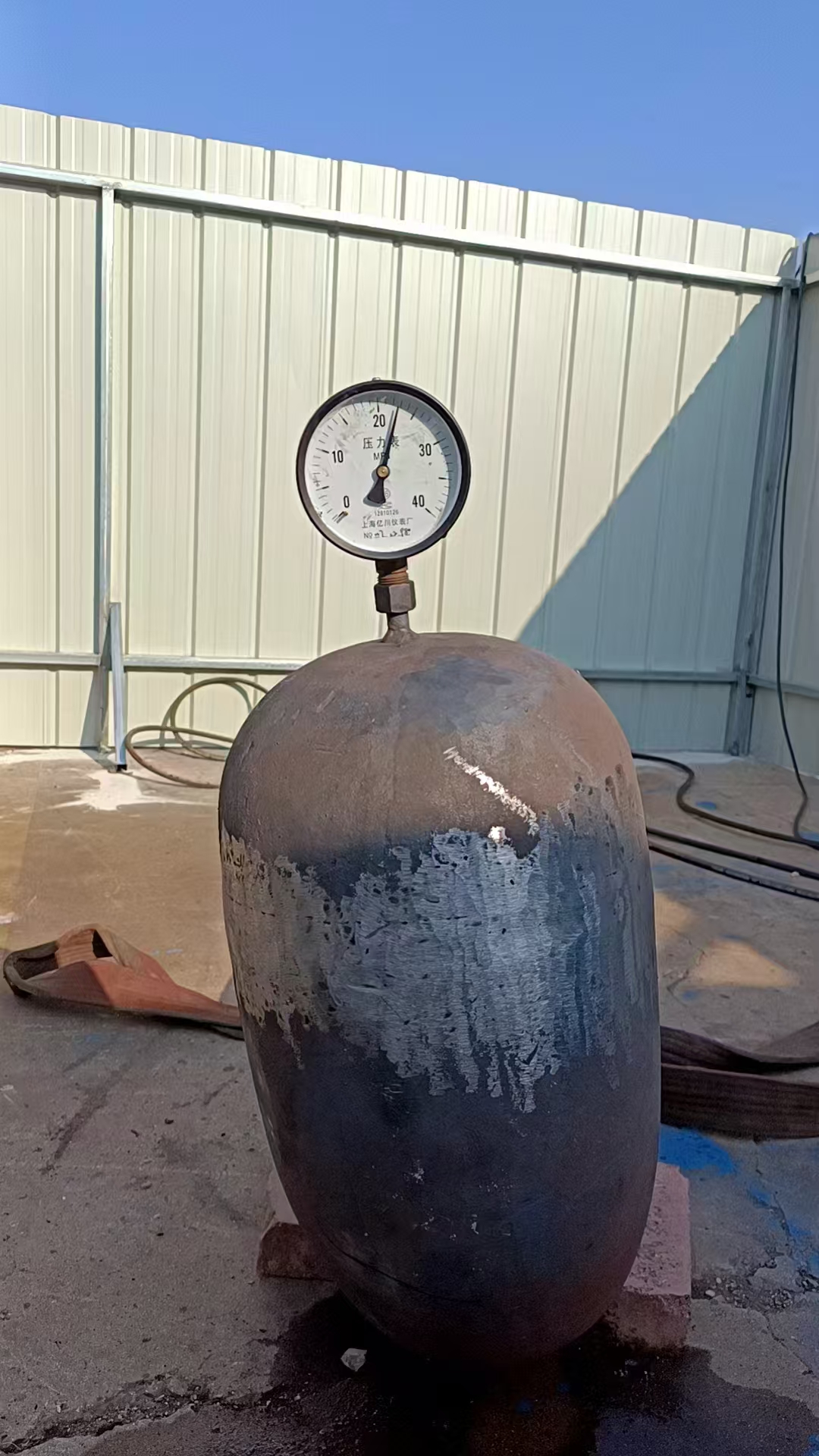
Scope of application
Pressure vessels: Pressure vessels such as boilers and gas tanks need to undergo hydraulic pressure tests after manufacturing or after maintenance to ensure that they can safely withstand the working pressure.
Pipeline systems: Pipelines that transport various media such as water, oil, and gas are subjected to hydraulic pressure tests after laying or modification to check the sealing of the pipelines and prevent medium leakage
- International Standard
- ASME Boiler and Pressure Vessel Code
- For the power boiler part of Volume I, detailed water pressure test procedures and pressure calculation methods are specified. The determination of the test pressure is related to factors such as the design pressure and maximum allowable working pressure of the boiler.
- The temperature of the test water is required to be controlled within the appropriate range to prevent brittle fracture. During the test, the various parts of the boiler, including the shell, pipe connections, welds, etc., should be checked for leaks or excessive deformation.
- ISO 15614-1:2017 “Specification and Qualification of Welding Procedures for Metallic Materials Part 1: Arc and Gas Welding of Steel, Arc Welding of Nickel and Nickel Alloys”
- In the water pressure test part of the welding procedure assessment, it is specified that the calculation principle of the test pressure is usually based on the design pressure.
- It is required to record the test data in detail during the test, including pressure, time, temperature, any leaks or