- Test Introduction
-This includes destructive testing such as bending testing, tensile testing, impact testing, hardness testing, as well as non-destructive testing such as visual inspection, radiographic testing, ultrasonic testing, magnetic particle testing, liquid penetrant testing, and other methods. - Purpose and process of non-destructive testing
-The purpose includes discovering indications, identifying and measuring discontinuities, evaluating defects, repairing defects, and re inspecting, as well as preparing and maintaining inspection reports.
-The basic requirements include qualified manpower, equipment calibration, and correct procedures. - Non destructive testing methods
-Visual Inspection (VT): The principle is to use eyes and instruments, including magnifying glasses, etc. It is suitable for welds with surface discontinuities. It is economical and convenient, but limited to external or surface conditions and the vision of the inspection personnel. Can be used to measure various characteristics such as quantity and size.
-Liquid penetrant testing (PT): based on capillary action to detect surface discontinuities, it is necessary to clean penetrant, wash, dry, and apply developer. The equipment includes penetrant, developer, etc. It is suitable for weld defects of surface openings. It is portable and relatively inexpensive, but the surface facial mask may mask defects. Parts need to be cleaned before and after testing.
-Magnetic Particle Testing (MT): Based on magnetic flux leakage detection of discontinuities, the equipment includes electrodes, magnetic yokes, etc. It is suitable for most surface discontinuities and some large gaps slightly below the surface, and is suitable for detecting cracks. It is relatively economical and convenient, but only suitable for ferromagnetic materials. Parts need to be cleaned before and after testing, and thick coatings may mask defects.
-Radiographic testing (RT): including gamma ray and X-ray testing, the principle is that the difference in absorption of radiation by objects leads to changes in film density. The equipment requirements vary depending on the type of radiation, and are suitable for welds with a large number of discontinuities. They can detect pores, incomplete fusion, etc. The advantage is that they are not limited by material type and grain structure, have surface and subsurface detection capabilities, and provide permanent records. However, planar discontinuities need to be aligned with the radiation beam, which is harmful to radiation, costly, and time-consuming to obtain results.
-Ultrasonic testing (UT): The principle is that the sound beam is reflected by the defect and displayed on the oscilloscope to display the signal. The equipment includes pulse echo instruments, etc. It is suitable for most weld discontinuities and is sensitive to planar discontinuities. The test results are available immediately and portable, but the surface conditions need to be suitable for transducer coupling, requiring coupling agents. Small and thin welds are difficult to detect and require reference to standards and skilled operators. - Detecting symbols
-This article introduces the relevant content of non-destructive testing symbols, including inspection frequency, reference line length, testing methods, various identification methods such as arrow side and other side, as well as symbol representations for different combinations of testing methods.
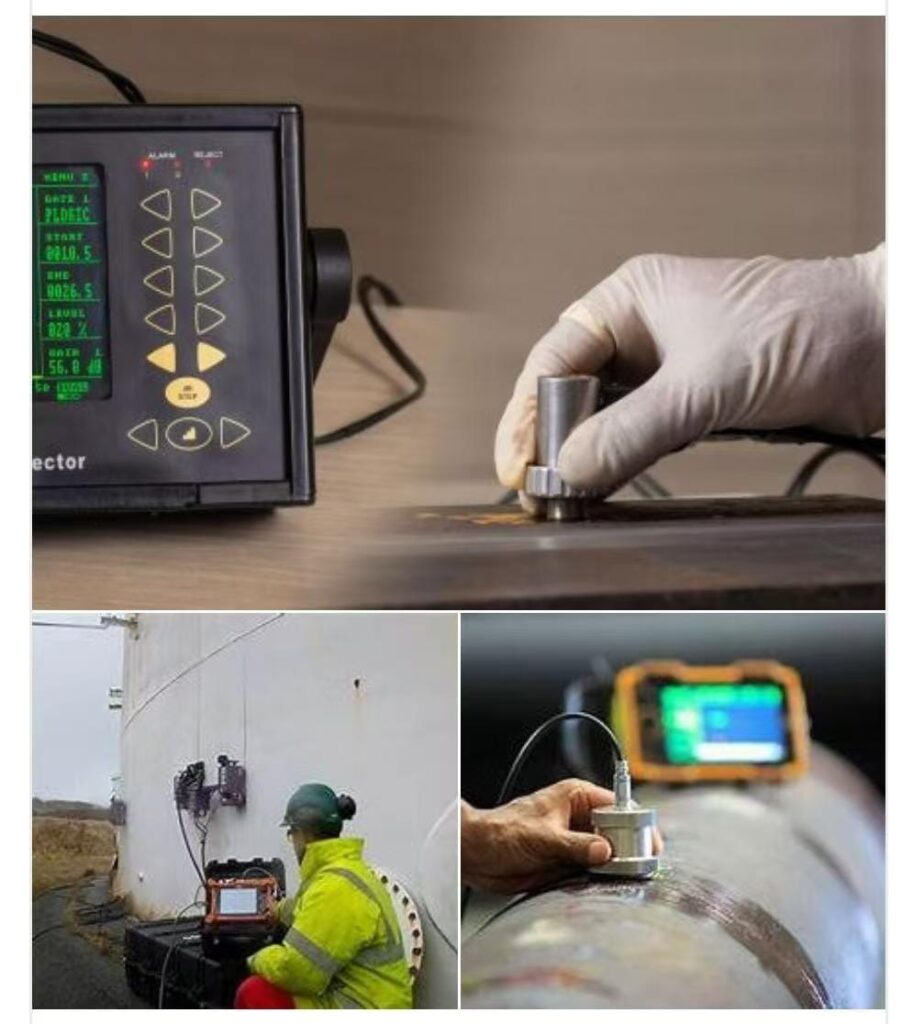
Purpose of Inspection
1.Doing Inspection (NDT) and finding Indications
2.Interpretation:Identifying and measuring discontinuties from indications
3.Evaluation thediscontiouties by acceptance criteria and identifying defects
4.Repair the defects and reinspection
5.Preparing ad maintaining inspection report
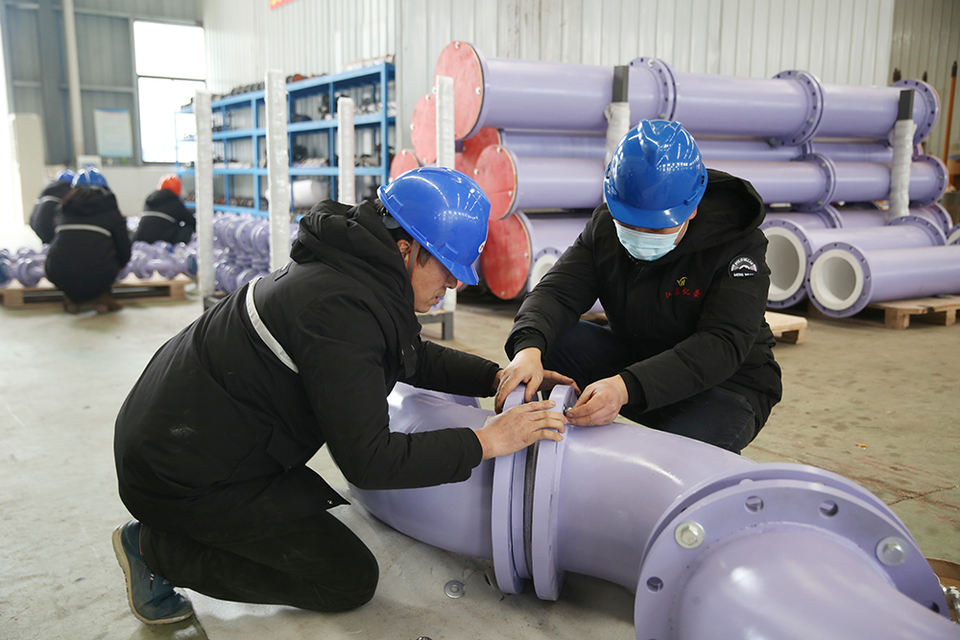
Basic TerminoIogy
■ Indication
■ Discontinuities
■ Defect
■ Interpretation / EvaIuation
■ Acceptance standard
■ codes / standards / specification
■ Latest / AppIicabIe codes
NDT Methods
■ surface
. VisuaI Testing (VT)
. Liquid penetrant Testing (pT) . Magnetic particIe Testing (MT)
■ VoIumetric
. Radiographic Testing (RT) . UItrasonic Testing (UT)
VisuaI Testing
■ principIe: use of eye & instruments
■ EquiPments Need: Magnifiers, coIor enhancement, projectors, other measurabIe instruments i.e. ruIers, micrometers, opticaI comparators, Iight source
■ APPIication: weIds which have discontinuities on surface
■ Advantages: EconomicaI, expedient, requires reIatively IittIe training & reIatively IittIe equipment for many
AppIications
■ Limitations: Limited to externaI or surface conditions onIY. Limited to visuaI acuity of inspector
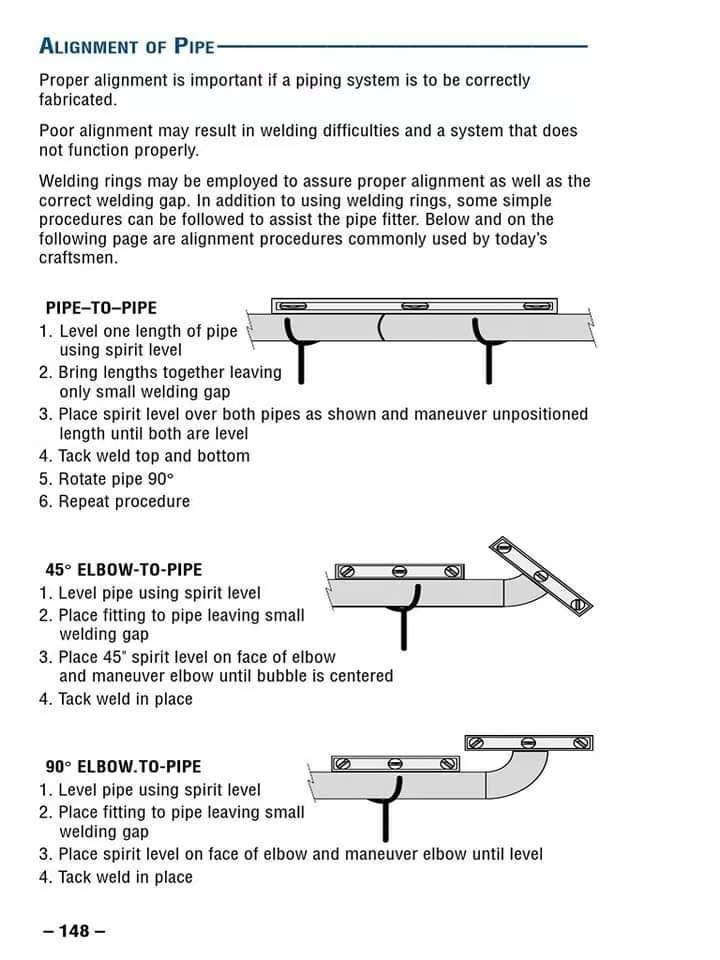
Magnetic particIe
■ Equipment: prods, yokes, coiIs suitabIe for inducing
magnetism into the weId.
power source (eIectricaI)
Magnetic powders, some
appIication require speciaI
faciIities and uItravioIet Iight.
Magnetic particIe
■ Advantages: ReIatively economicaI and expedient,
Inspection equipment is considered portabIe. unIike dye penetrants, magnetic particIe can detect some
discontinuities sIightIY beIow the surface can be used for higher temperatures.
■ Limitations: AppIicabIe only to ferromagnetic materiaI. parts must be cIeaned before and after inspection. Thick coatings may mask rejectabIe discontinuities. some
appIications require parts to be demagnetized afterinspection. Magnetic particIe inspection requires use of eIectricaI energY for most appIications
MT
Based on principIe of attraction of magnetic particIes to fIux Ieakage
For Magnetic MateriaIs
For surface and sub-surface detect detection
Quick & Fast
can detect incIusions& foreign
materiaI entrapment
Easy post cIeaning
Best method for detecting stress corrosion cracks & fatigue crack
PT
Based on principIes of capiIIary action
For aII materiaIs
onIy for surface detection
sIower process
cannot detect such defects
subsequent cIeaning(post cIeaning) troubIe
Radiography (Gamma)
RadiograPhy (Gamma)
■ APPIication: weIds which have voIuminous discontinuities such as porosity, incompIete joint penetration, corrosion etc ,LameIIar type discontinuities such as cracks and
incompIete fusion can be detected with a Iesser degree of reIiabiIity. May aIso be used in certain appIications to evaIuate dimensionaI requirementsuch as fit-up, root conditions, and waII thickness.
■ Advantages: GeneraIIY not restricted bY tYpe of materiaI or grain structure. surface and subsurface inspection
capabiIitY. Radiographic images aid in characterizing discontinuities provides a permanent record for future review.
■ Limitations: pIanar discontinuities must be favorabIY
aIigned with radiation beam to be reIiabIY detected;radiation poses a potentiaI hazard to personneI. cost
radiographic equipment, faciIities, safetY programs, and reIated Iicensing is reIativeIy high. A reIativeIy Iong time between exposure process and avaiIabiIity of resuIts.AccessibiIitY to both sides of the weId required.
Radiography (X-rays)
■ Advantages: AdjustabIe energy IeveIs. GeneraIIy produces higher quaIity radiographs than gamma sources. AIso same advantages as above.
■ Limitations: High initiaI cost of x-ray equipment. Not generaIIy considered portabIe. AIso, same Iimitations as above.
UItrasonic Testing
■ Equipment needs: PuIse-echo Instrument capabIe of exciting a piezoeIectric materiaI and generating
uItrasonic energy within a weId, and a suitabIe cathode ray tube scope capabIe of dispIaying the magnitudes of received sound energy. caIibration standards, Iiquid coupIant.
UItrasonic Testing
■ AppIication: Most weId discontinuities incIuding cracks, sIag and incompIete fusion. Can aIso De used to verify weId thickness.
■ Advantages: Most sensitive to pIanar type discontinuities. Test resuIts known immediateIy. portabIe. Most uItrasonic fIaw detectors do not require an eIectricaI power outIet. High penetration capabiIity.
■ Limitations: surface condition must be suitabIe for coupIing of transducer. CoupIant (Iiquid) required. smaII thin weIds may be difficuIt inspect. Reference standards are required. Requires a reIativeIy skiIIed operator or inspector.
UT Techniques
■ Two basic techniques are used in Iocating and evaIuating anguIar fIaws Contact testing Immersion testing
■ The shape or surface condition of a discontinuity infIuences the indication on the CRT.
■ A discontinuity having a rough surface wiII tend to scatter the refIection as compared to a smooth fIaw.
■ NonmetaIIic incIusions are typicaIIy rough and wouId scatter the sound more than a crack-Iike discontinuity.
UT
■ For internaI & surface defects
■ More suitabIe for pIaner (two dimensionaI defects
■ AccessibiIity from one side
■ size and Iocation of the defect can be judged quite
accurateIy
■ Better sensitivity & resoIution
■ possibIe to test higher
thickness, up to 5 meters
■ operator skiII is important
■ No safety probIem
■ Faster resuIts
RT
■ For internaI defects
■ possibIe to detect onIy voIuminous (3D) defects
■ AccessibiIity from both sides
■ It is difficuIt to judge the size & Iocation of defects
■ poor sensitivity
■ Thickness Iimitations, a few inches
■ Easy operation
■ safety precautions are mandatory
■ sIower resuIts in fiIm radiography. on Iine radiography very costIy
SeIection of a particuIar NDT technique
■ Advantages/Limitations of methods
■ Acceptance standard
■ Cost
■ Manufacturing technoIogy ■ Type of discontinuities
■ physicaI Condition of the job
■ Need of quaIified engineer/technician