Quality control (QC) is a crucial link in enterprises, primarily responsible for ensuring that product quality meets established standards and requirements. In the definition of ISO 8402:1994, quality control is described as “the operational techniques and activities adopted to achieve quality requirements”. In order to implement and comply with ISO9000 standards, many organizations will establish specialized departments or positions to be responsible for functions related to quality control. These personnel responsible for QC work play a crucial role in the enterprise, and their duties include inspecting incoming goods, production processes, final products, and shipments to ensure the stability and reliability of product quality.
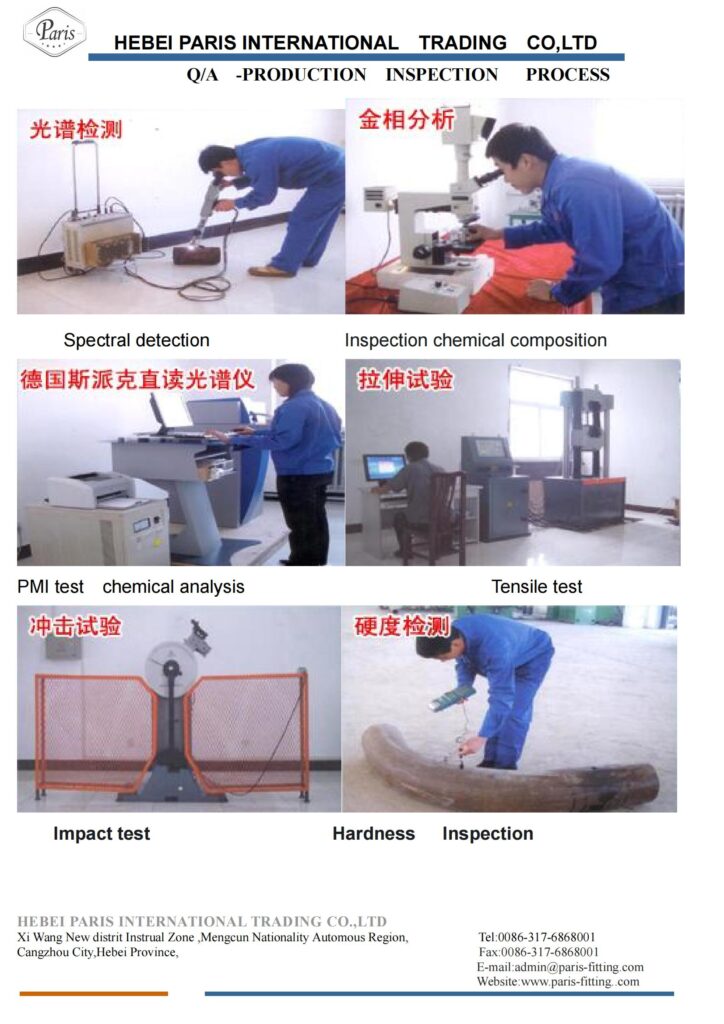
Produce process control
Quality control during the product development and design phase is called quality design. In manufacturing, it is necessary to monitor the production process, which is called the quality monitoring stage. Controlling quality through sampling inspection is a traditional quality control method, known as post quality control. The most important stage in the above mentioned stages is quality design, followed by quality monitoring, and then post quality control. For production processes with lower quality levels, post inspection is essential, but quality control should be the source control, and the earlier the prevention, the better
To ensure product quality, it is necessary to strengthen the quality control of the production process. Quality control is the operational techniques and activities adopted to meet quality requirements. Its purpose is to monitor the process and eliminate factors that cause dissatisfaction in all stages of the quality environment, in order to ensure product quality
Quality control steps
1. Select the control object;
2. Select the quality characteristic values that need to be monitored;
3. Determine specification standards and provide detailed descriptions of quality characteristics;
4. Select monitoring instruments or self-made testing methods that can accurately measure the characteristic value or corresponding process parameters;
5. Conduct actual testing and keep records of data;
6. Analyze the reasons for the differences between reality and specifications;
7. Take corresponding corrective measures. After taking corresponding corrective measures, the process still needs to be monitored to maintain it at a new level of control. Once a new influencing factor appears, it is necessary to measure the data and analyze the reasons for correction.
Therefore, these 7 steps form a closed process called the “feedback loop”. This has similarities with the DMAIC of the 6Sigma quality breakthrough mode.
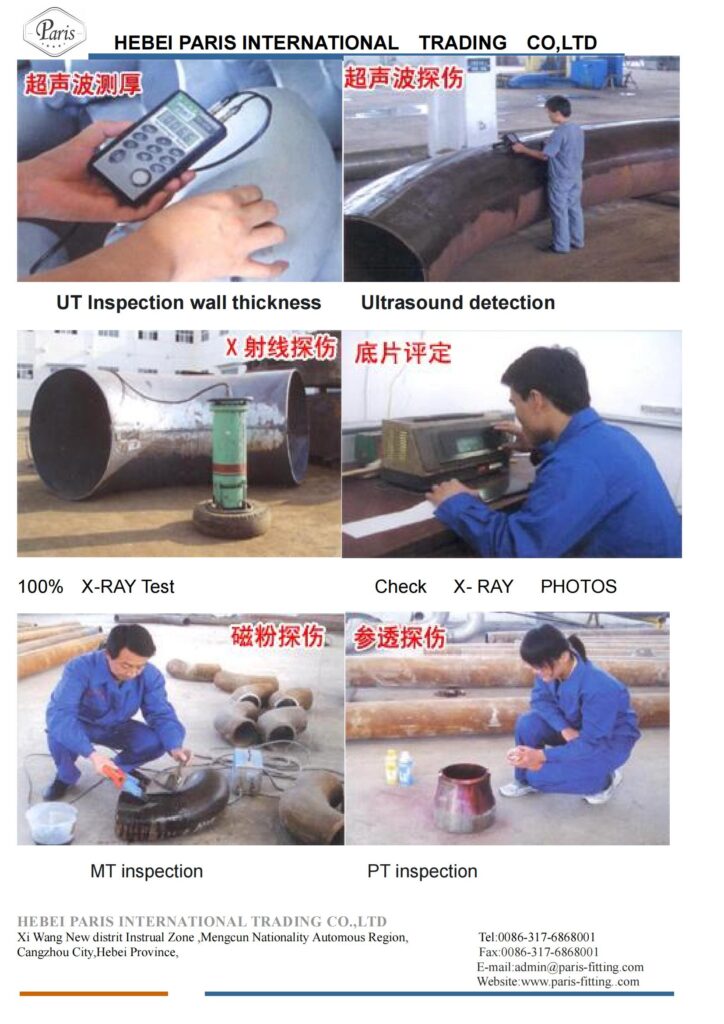
Witness point
(1) The construction unit shall notify the supervising engineer in writing at a certain time before arriving at a certain witness point, stating the preparation time for construction at that witness point, and requesting the supervising personnel to witness and supervise on site at that time.
(2) After receiving the notification, the supervising engineer should indicate the date of receipt of the notification on the “Construction Tracking File” and sign it.
(3) Supervisors should witness on-site at the agreed time. Supervisors should supervise and inspect the implementation process of witness points, and make detailed records on the witness form before signing.
(4) If the supervising personnel fail to witness within the specified time, the construction unit may consider that it has been approved by the supervising engineer and has the right to carry out the construction.
(5) If the supervisory personnel have already arrived at the site for inspection before this and have written relevant opinions on the “construction tracking file”, the construction unit should specify the improvement measures taken or specific opinions
Stop point
The stopping point is a quality control point that is more important than the witnessing point, usually for “special processes” or “special processes”. Any control object listed as a stopping point must notify the supervising party to send personnel to monitor the control point before the specified control point arrives. If the supervising party fails to supervise and inspect the site at the agreed time, the construction unit should stop entering the corresponding process of the control point and wait for the supervising party according to the contract. Without approval, activities cannot continue beyond the point. It is usually approved in writing to proceed, but it can also be approved to proceed according to an agreed authorization system.
Witness points and stopping points are usually specified by the engineering contracting unit in the quality plan, but the construction unit should submit the construction plan and quality to the supervising engineer for approval. If the supervising engineering has different opinions on the setting of witness points and stops, the construction unit should be notified in writing, requesting modifications, and then submitted to the supervising engineering for approval before implementation
Control basis
- Contract documents
- Design documents
- Legal and regulatory documents related to quality management issued by relevant departments of the client’s country and government
- Specialized technical regulatory documents related to quality inspection and control