Intergranular corrosion test is a test used to detect the sensitivity of metal materials, especially alloys such as stainless steel, to intergranular corrosion under specific environments.
The principle is that due to the differences in chemical composition and physical state between the grain boundary and the interior of the grain, the grain boundary of the metal may be corroded first under the action of the corrosive medium.
Common intergranular corrosion test methods include:
- Sulfuric acid-copper sulfate-copper chips method (Strauss test): The sample is immersed in a sulfuric acid-copper sulfate solution, copper chips are used as a catalyst, and the test is carried out for a certain period of time under boiling state, and then observed or bent to check whether there are intergranular corrosion cracks.
- Nitric acid method: The sample is boiled in a nitric acid solution, and different stainless steel materials are tested according to the corresponding standards for the time. After completion, the corrosion rate and other indicators are compared to determine the intergranular corrosion tendency.
These experiments can help determine the quality of metal materials and select suitable materials for specific corrosive environments, which is important for ensuring the safe use of materials in chemical, marine and other fields.
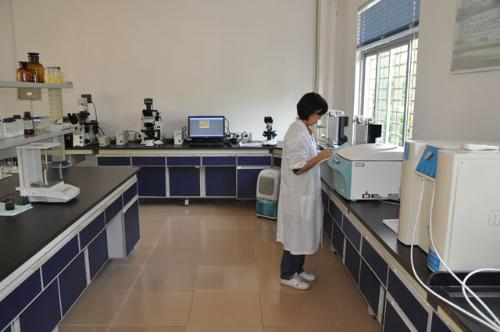
Scope of application
- Stainless steel materials: such as 304, 316 and other stainless steels, which are widely used in food processing, chemical equipment, medical equipment and other fields. Through intergranular corrosion experiments, it is ensured that it will not be damaged by intergranular corrosion when it comes into contact with corrosive media (such as acidic components in food, acid and alkali solutions in chemical industry).
- Nickel-based alloys: Nickel-based alloys used in high temperature and strong corrosive environments, such as hot end parts of aerospace engines and high-temperature reaction devices in petrochemicals, also need to undergo intergranular corrosion experiments to verify their corrosion resistance.
Methods for judging qualified
- Bending method: This is a more commonly used method. Bend the test specimen after the test. If there are no cracks on the surface of the specimen, it is generally considered that the material is qualified in terms of intergranular corrosion. For example, for stainless steel sheet specimens, after bending to the specified angle (such as 180°) according to the standard requirements, observe whether there are cracks on the outer surface of the bent part.
- Metallographic inspection method: Observe the grain boundary state of the specimen through a metallographic microscope. If no obvious corrosion marks are found at the grain boundary or the corrosion depth is within the specified qualified range, it is judged to be qualified. For example, it is stipulated that the depth of intergranular corrosion shall not exceed a certain value (such as 10μm). When the observed corrosion depth is less than this value, the material is qualified.
- Weight method: Compare the weight change of the sample before and after the test. After immersion in the corrosive medium for a certain period of time, if the weight loss is within the allowable range, it can also be judged as qualified. For example, it is stipulated that the weight loss per unit area shall not exceed a certain value (such as 1mg/cm²). When the weight loss after the experiment is lower than this standard, the material meets the requirements.
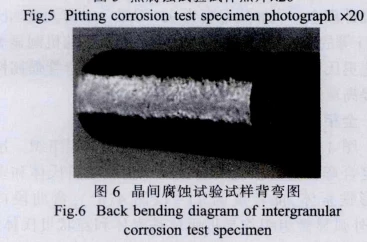
. International standards:
- ISO 3651-1:1998: Applicable to austenitic and austenitic-ferritic duplex stainless steels. It mainly specifies the general requirements and methods for intergranular corrosion tests of such stainless steels and is one of the internationally recognized intergranular corrosion test standards.
- ISO 3651-2:1998: Applicable to ferrite, austenitic, austenitic-ferritic duplex stainless steels and welded parts, and standardizes the intergranular corrosion tests of these materials, providing specific guidance on the evaluation and test methods of intergranular corrosion.
2. American standards: - ASTM A262-2015: It is a standard developed by the American Society for Testing and Materials for the detection of intergranular corrosion of metal materials such as stainless steel, nickel-based alloys and titanium alloys. The standard includes five different test methods, such as A, B, C, E and F, which are respectively applicable to different types of metal materials and different test conditions.
- ASTM G28-2002(2008): “Standard Test Method for Inspection of Intergranular Corrosion Susceptibility of Forged High Nickel-Chromium Bearing Alloys”, mainly for the test of forged high nickel-chromium bearing alloys’ susceptibility to intergranular corrosion.
- Chinese Standards:
- GB/T 4334-2020: specifies the test specimens, test solutions, test equipment, test conditions and procedures, test result evaluation and test reports for the test method of intergranular corrosion of stainless steel. It includes six intergranular corrosion detection methods, such as 10% oxalic acid etching test method (Method A), sulfuric acid-ferrous sulfate corrosion test method (Method B), 65% nitric acid corrosion test method (Method C), nitric acid-hydrofluoric acid corrosion test method (Method D), sulfuric acid-copper sulfate corrosion test method (Method E), and stainless steel 5% sulfuric acid corrosion test method (Method F).
- GB/T 7998-2005: “Determination Method for Intergranular Corrosion of Aluminum Alloys”, applicable to intergranular corrosion tests of aluminum alloy materials.
- GB/T 15260-2016: “Corrosion of Metals and Alloys – Intergranular Corrosion Test of Nickel Alloys”, specifies the methods and requirements for intergranular corrosion tests of nickel alloys.
- GB/T 21433-2008: “Intergranular Corrosion Sensitivity Test of Stainless Steel Pressure Vessels”, mainly for intergranular corrosion sensitivity test of stainless steel pressure vessels, to ensure the safety of pressure vessels during use.
- Japanese Standard:
JIS G0571: is an intergranular corrosion test method standard, applicable to metal materials such as stainless steel, nickel-based alloys and titanium alloys. This standard specifies requirements for sample preparation, test conditions, test methods, and evaluation of test results.
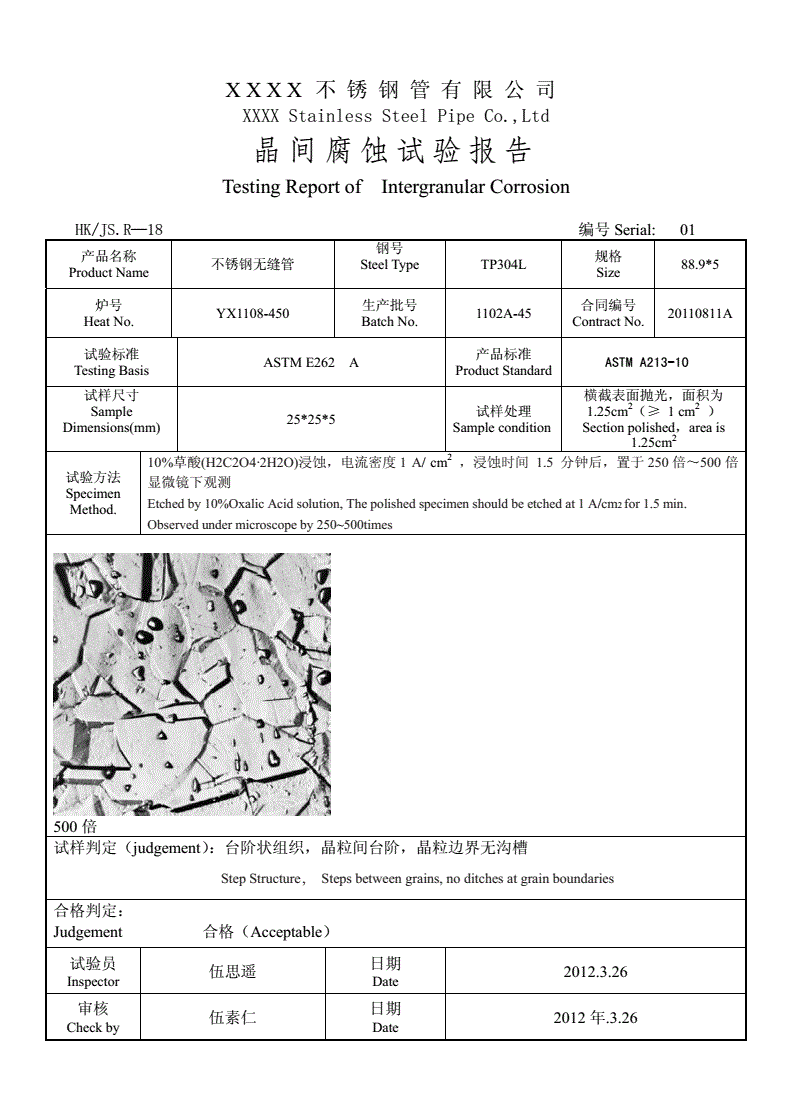
The test report mainly includes the following contents:
Name, size and area of the sample;
If sensitized, the sensitization treatment system should be recorded; Test time; Weight of the sample before and after the test;
Corrosion rate of each cycle of the sample [g/(m².h)]; f) Ratio of corrosion rates.Test evaluation method:
Surface metallographic evaluation; Corrosion rate evaluation; Bending evaluation;